半導體製程 | ||||||||||||||||||||||||||||||||||||||||||||
---|---|---|---|---|---|---|---|---|---|---|---|---|---|---|---|---|---|---|---|---|---|---|---|---|---|---|---|---|---|---|---|---|---|---|---|---|---|---|---|---|---|---|---|---|
|
||||||||||||||||||||||||||||||||||||||||||||
電晶體數量 |
||||||||||||||||||||||||||||||||||||||||||||
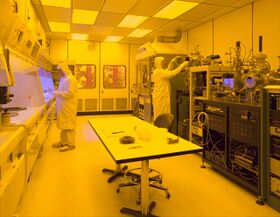
半導體製程是被用於製造晶片,一種日常使用的電氣和電子元件中集成電路的處理製程。它是一系列照相和化學處理步驟,在其中電子電路逐漸形成在使用純半導體材料製作的晶片上。矽是今天最常用的半導體材料,其他還有各種複合半導體材料。從一開始晶圓加工,到晶片封裝測試,直到出貨,通常需要6到8周,並且是在晶圓廠內完成。
晶圓
典型的晶片是用極度純淨的矽以柴可拉斯基法、泡生法等方式長成直徑12吋(300毫米)的單晶圓柱錠(梨形人造寶石)。這些矽碇被切成晶片大約0.75毫米厚並拋光為非常平整的表面。
一旦晶圓準備好之後,很多工藝步驟對於生產需要的半導體集成電路是必要的。總之,這些步驟可分成四組:
- 前端製程
- 後端製程
- 測試
- 封裝
製程
在半導體製程中,不同的生產工序可歸為如下四類:沉積、清除、製作布線圖案、以及電學屬性的調整。
前端製程
"前端製程"指的是在矽上直接形成電晶體。雙極二極體,mos管等
二氧化矽
金屬層
互聯
晶片測試
晶片處理高度有序化的本質增加了對不同處理步驟之間度量方法的需求。晶片測試度量裝置被用於檢驗晶片仍然完好且沒有被前面的處理步驟損壞。當一塊晶片測量失敗次數超過一個預先設定的閾值時,晶片將被廢棄而非繼續後續的處理製程。
元件測試
封裝
步驟列表
- 晶片處理
有害材料標誌
許多有毒材料在製造過程中被使用。這些包括:
工人直接暴露在這些有毒物質下是致命的。通常IC製造業高度自動化能幫助降低暴露於這一類物品的風險。
歷史
當線寬遠高於10微米時,純淨度還不像今天的元件生產中那樣至關緊要。但隨着元件變得越來越整合,無塵室也變得越來越乾淨。今天,工廠內是加壓過濾空氣,來去除哪怕那些可能留在晶片上並形成缺陷的最小的粒子。半導體製造產線裏的工人被要求穿着無塵衣來保護元件不被人類污染。
在利潤增長的推動下,在1960年代半導體元件生產遍及德薩斯州和加州乃至全世界,比如愛爾蘭、以色列、日本、中國台灣、韓國和新加坡,且在今天已是一個全球商業。
半導體生產商的領袖大都在全世界擁有產線。英特爾,世界最大的生產商之一,以及在美其他頂級生產商包括台積電(台灣)、三星(韓國)、德州儀器(美國)、超微半導體(美國)、聯電(台灣)、東芝(日本)、NEC電子(日本)、意法半導體(歐洲)、英飛凌(歐洲)、瑞薩(日本)、索尼(日本),以及恩智浦半導體 (歐洲)在歐洲和亞洲都有自己的裝置。
在2006年,在美國有大約5000家半導體和電子零件生產商,營業額達1650億美元[1]。
參考文獻
外部連結
- 半導體製造 - www.SiliconFarEast.com
- Intel's Animated step-by-step process
- NEC Electronics' Virtual Factory Tour
- 半導體 Glossary
- 半導體材料製程
- 矽熱氧化計數機
參見
- 微製造
- 電子設計自動化
- Fab
- Foundry (electronics)
- GDS-II
- OASIS
- SEMI — 半導體工業的行業組織
- 原子層沉積
- 國際半導體技術發展藍圖